COMPLETE ENGINEERED PLUG N PLAY POWERTRAINS FOR SPECIFIC APPLICATIONS -> COMPLETE ENGINEERED PLUG N PLAY POWERTRAINS FOR SPECIFIC APPLICATIONS
- By Admin
- •
- 04 Aug, 2020
- •
VW Van and Bug kits
COMPARED TO COMPETITOR KITS
-> Our kits really do come pre-wired with only plugs to plug into and ready to drop into donor vehicles vs. most competitor kits are not pre-wired, all wire/cable and connectors/terminals are loose, so customer needs to cut and make all wire harnesses
-> Kits come with a complete installation video to show the customer how to install kit themselves step by step vs. most competitor kits that simply sell you a pallet of components with a wiring diagram, but no real instructions on how exactly to properly create all wired connections, mount all parts, sequence of operations and start-up of the powertrain, etc.
-> Kit has a BMS based ESS to maintain and extend battery life, a large part of the kit cost/ investment by the customer
-> More Energy for more Range with ~32 kWh ESS and higher quality battery cell tech using high performance 18650 cells vs. most competitor kits use only ~22kWh consisting of low energy density ( heavier for same energy) LiFePO4 prismatic cells
-> Higher system voltage for more efficiency of 144Vdc vs. ~96Vdc most competitors use
SE40V2.0 144Vdc Electric Outboard kit – Ideal for powering vessels under 20 feet such as RIBs, Pontoon boats Jon boats, where 40hp gas outboards are used for up to ~30mph.
Specs: 40hp/30kW at the prop. 20″ shaft length. Battery system (ESS) 144Vdc nominal – should be minimum ~26kWh (can be less for low performance duty cycle applications), 200 Amp continuous, 300 Amp peak (not included in this package) – max 180Vdc charging top-off. 179lb/81kg total weight. Electric trim and tilt. Liquid-cooled controller and brushless PMAC motor (same as used in our QWC/SEV-55kW peak drive subsystem kit) Bluetooth wireless app. Lower unit is a version of a Yamaha compatible design so all traditional lower unit parts can be purchased at your local Yamaha parts dealer. Throttle and custom cable set also included in this package. Here’s the best part, this electric outboard has all the power of the market leader “Deep Blue 40” at the approximate price range of the market leader Cruise 10.0, finally an affordable solution! (NOTE: When ordering, we will need to get specific boat length for custom cable set that is included in package. Boat should be under 1,000 lbs gross vehicle weight with e-outboard, ESS passengers and cargo and transom rated for at least 40hp.)
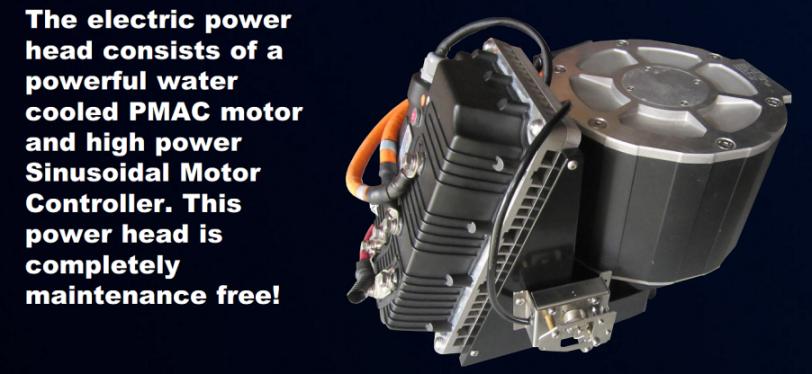
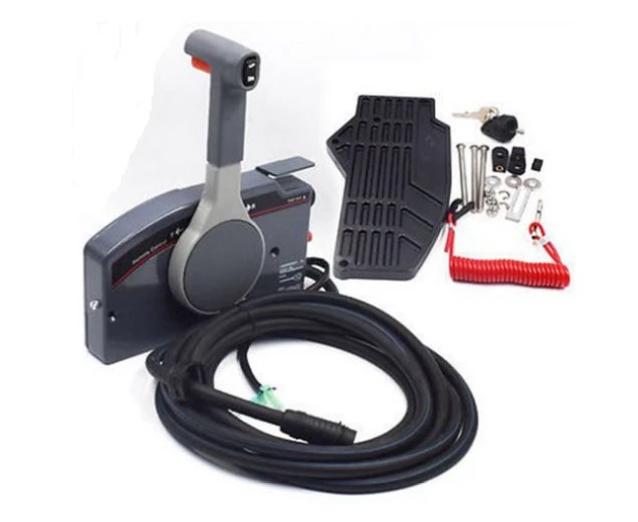

Complete systems with 26~32kWh, 200 Amp continuous, 300 Amp peak, lithium-ion marine battery system (ESS) are available as well. This Electric Outboard can be run at lower throttle settings with smaller capacity ESS (energy storage systems a.k.a. the battery system) for less running times.
Buying Old Outboard Technology Is Going To Cost You More In the Long Run Than a Clean, Powerful, Maintenance-free Electric Outboard system.
Contact us for more complete plug ‘n play kits in various stages of development
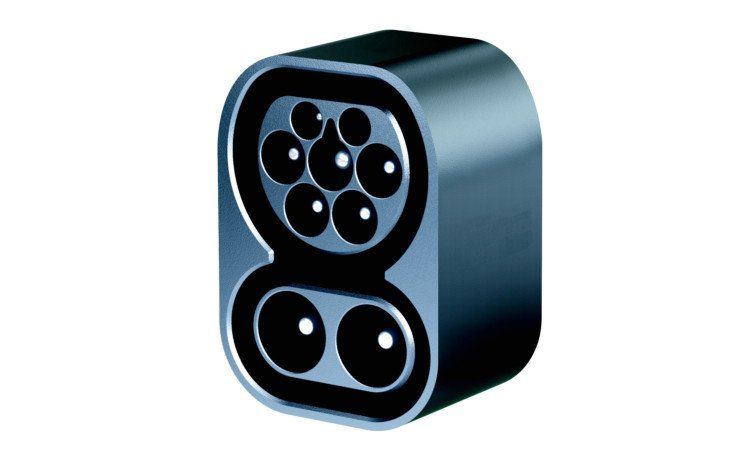
by S.E.Tice …
Which DC Fast Charger Standard will win, or will regions have to have multiple standards, or will the world be divided into regions using different standards?
UPDATE on Porsche Fast Charging – see below
There are four main DC Fast Charger (a.k.a. DCQC – DC Quick Charge) contenders:
- CHAdeMO used worldwide – 40-60kW limit, with tech upgrades 100kW possible
- CCS (Combined Charging System) – two versions (different in North America and Europe, rest of the world uses one of version depending on the market) – used by BMW, GM, VW, and other carmakers – 50kW typical, 350kW possible.
- Tesla Superchargers – two versions (different in North America and Europe/rest of the world) – up to 120kW
- GB/T China – only used in China – BYD among other Chinese companies use this. Mahindra and Tata electric cars also use this standard – 50kW typical – over 150kW possible.
Tesla DC Fast Charger is proprietary for good reason – Tesla built their own SuperCharger network around the world, but do the rest of the vehicle OEMs have to support multiple standards especially when the CapEx to install these chargers is nontrivial? World map Overview of AC and DC 3 Levels
Here are the connectors and inlet s – most promising is the CCS Type 2 shown below (See below, Porsche makes its choice for DC Fast charger standard)
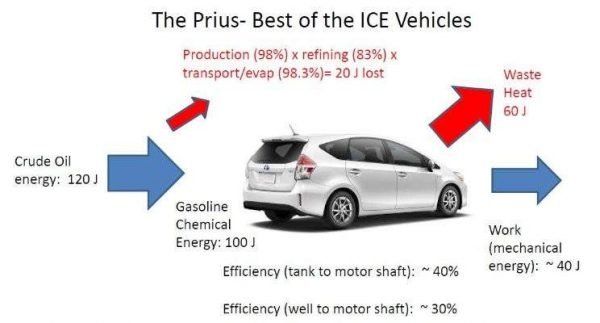
by S. E. Tice…
“The conclusion is that All-Electric Vehicles (BEVs) beat the fleet average ICE vehicle hands down in every group of states they evaluated, on a full lifecycle emissions basis, and in fact they outperform the Prius (52 mpg (4.5 L/100km)) in most states. In the most populous states, BEVs beat the Prius by a substantial margin. And that result is going to get nothing but better in future.” “overall Prius source to wheels efficiency at 0.8*0.38 = about 30% efficiency. And that’s the best ICE car you can buy…even fueled by a modern gas power plant”
Good analysis and article by Paul Martin, Chemical process development expert, and EV and renewable energy advocate, on all-electric vehicles vs the highest efficiency hybrid vehicle available today. https://www.linkedin.com/pulse/energy-cycle-efficiency-vehicles-does-ev-really-win-paul-martin/
Another good article by Paul Martin which developed some of the analysis data for the above article. https://www.linkedin.com/pulse/so-exactly-how-much-electricity-does-take-produce-gallon-paul-martin/
New data from the US EPA on power plant greenhouse gas emissions are in, and electric vehicles (EV) in the US are even cleaner than they were before. The climate change emissions created by driving on electricity depend on where you live, but on average, an EV driving on electricity in the U.S. today is equivalent to a conventional gasoline car that gets 80 MPG, up from 73 MPG in our 2017 update. As grids get greener, and EVs also become more efficient, the so-called “long tailpipe” of the EV gets shorter and shorter. In all states except Hawaii, an efficient EV beats the most efficient ICE hybrid vehicle- in some locations by a factor of 3!
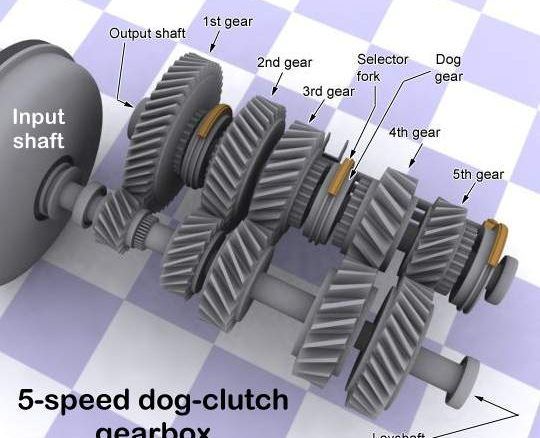
In some cases multi-speed gearboxes must be used; for example for extreme performance (acceleration/top-speed), heavy load/steep grades trucking, off-road high load/grade applications.
SOME BENEFITS OF MULTI-SPEED GEARBOXES
– keeps e-motor(s) in higher efficiency range improving overall efficiency of EV powertrain to deliver more range, or alternatively same range with a smaller battery pack, hence cost and weight reduction of the powertrain.
– lower torque motor can be used which results in cost benefits and an overall reduction in the weight of the powertrain or alternatively, with same motor, it can deliver better performance at higher level of efficiency.
– offer better launch acceleration, lower noise and a higher cruising speed, while the hill climbing ability of utility vehicles can be improved.
– simpler, lighter and cheaper power electronics, and because the motor can be kept within its optimum speed range there’s less wear.
– for both high acceleration requirements and extreme top speed requirements, to avoid extremely wide RPM e-motors/controllers, multi-speed is required.
– for extreme grade, terrain and carrying load requirements, multi-speed is required or the motor/controller sizing will not be cost-effective.
HOWEVER, if you are fortunate enough to be able to design your own optimized motors/controllers for specific mission “low duty” usage profiles, as Tesla does, single-speed gearboxes do come out ahead – however in some circles, the debate rages on whether multi-speed gearboxes can be justified to benefit these non-heavy duty applications. Another approach is rather than use multi-speed gearboxes, use front and rear motors with different single-speed ratios, than the control system directs more power to the motor with the better gear ratio for the specific situation.
SOME CASE STUDIES PROVE OUT THESE BENEFITS:
1 – DCT Transmission specialist Vocis’s simulations show that their 2-4SED two-speed configuration could reduce the battery energy consumed by up to 15%
(4SED tests reached 15%) over the industry-standard New European Drive Cycle, without any significant increase in overall cost or packaging volume, as well as extending battery life and providing the potential to substantially downsize the powertrain and battery pack.
The 4SED system resembles a dual-clutch transmission configuration, but with two motors instead of twin clutches. There are two input shafts, each driven by its own electric motor. The two motors replace the usual clutches and synchronisers, allowing the next gear to be preselected before the previous one has been disengaged, and can synchronise shaft speeds. Fewer software algorithms needed compared to a normal automated gearbox, and because there are no hydraulics, there is no need for valve control.
https://newatlas.com/new-multi-speed-electric-vehicle-transmission-improves-ev-performance-and-range/11670/
https://www.autoblog.com/2011/08/19/vocis-says-two-speed-electric-vehicle-transmission-will-boost-ba/
http://www.vocis.co.uk/2-speed-electric-minibus/
http://drivesncontrols.com/news/fullstory.php/aid/4036/Two-motor_powertrain__91can_raise_EV_efficiencies_by_15_25_92.html
http://user49750.vs.easily.co.uk/wp-content/uploads/2014/05/4SED-paper.pdf
2 – Zeroshift’s concept prevents any torque interruptions during ratio changes and does not require a clutch, an issue that may have deterred EV manufacturers from fitting multi-speed gearboxes. Zeroshift studies suggest that by using a compact, multi-speed transmission and a smaller electric motor, manufacturers can gain an operating efficiency of up to 10% or more. You can use that 10% to improve EVs’ range or reduce the size, weight and cost of battery packs. The benefits of Zeroshift’s transmission would be greatest for electric delivery vehicles where the compromises in efficiency are greatest. To be able to pull away fully laden on hills requires low gearing, but the motor then runs too fast and too inefficiently on the highway. Also Zeroshift is less expensive to manufacture than a continuously variable transmission (CVT) or a dual clutch transmission (DCT), says Bill Martin, Zeroshift’s managing director.
There are several motorcycle seamless shift systems available, but the Moto GP teams are keeping tight-lipped about whose technology they are using. Two British companies, Xtrac and Zeroshift, produce the technology, but neither is willing to confirm their involvement with a particular team. Zeroshift though was willing to explain the workings of its system.
http://www.zeroshift.com/
http://www.greencarcongress.com/2010/08/zeroshift-20100819.html
https://www.highpowermedia.com/blog/3212/motogp-transmissions
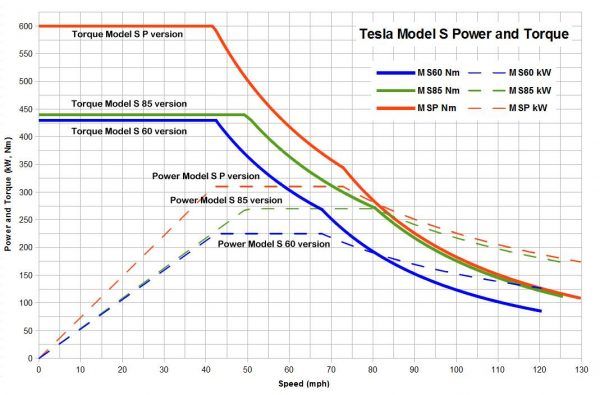
by S.E. Tice…
Why do electric powertrains not perform like ICE (internal combustion engine) powered ones in track situations? (however for drag racing, high performance electric vehicles do just fine). What’s this “throttling” all about w.r.t. BEV range, performance, and charging capability? Fielding questions like this, there seems to be continual “puzzlement” in comparing power obtainable from Electric (all-electric or BEV – battery electric vehicle) vs ICE powertrains, especially when one wants to drive the vehicle aggressively or in track applications. This article will attempt to explain some of the overview level issues in comparing the two types of vehicle powertrains.
In general, ICE powertrains, if properly cooled, can produce peak power and torque for longer durations than electric powertrains. Simply put, the power (horsepower – hp or kilowatts – kW) production chain for an electric powertrain looks like this -> battery system (ESS – energy storage subsystem) -> the controller(s)/inverter(s) -> electric motor(s). In general, these 3 main elements produce the motor shaft hp/kW (different than and usually greater than hp available at wheels). Only looking at a high power electric motor and its inverter/controller vs. a high power ICE, observe the power/torque vs. RPM curves below. For the electric powertrain, the Tesla Model S and Borg-Warner IPM (internal permanent) motor figure below also shows typical power vs. RPM trends.
High Power IPM Electric Motor based drive subsystem (top figure below) and Tesla Model S drive subsystem (dotted lines are power in kW) vs. high Power ICE (lower figure below)
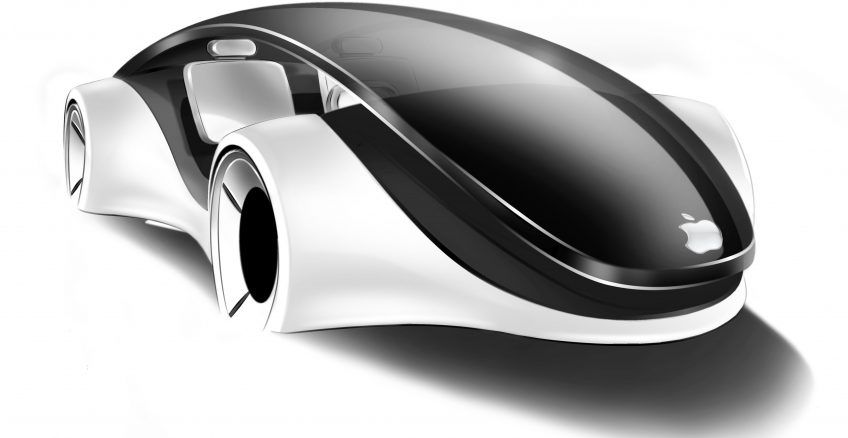
By Jason B. Hunt, guest contributor
A little while back, it was written that self-driving cars will need people, too. Studies have indicated that people are generally interested in if not excited by the chance to relax fully when riding in the self-driving cars of the near future. People want to read, nap, watch TV and movies, and potentially even consume alcohol while the automated car does all the work. Yet it was suggested that the desire for this sort of ride was likely somewhat ambitious. The logic was that even if an automated vehicle can handle itself 99% of the time without problems, that last 1% – amplified over tens of thousands, and eventually millions of drivers – would result in some real problems of unacceptable frequency.
That may in fact be the case, and it may not be a problem we can fix in the next few years. Apple, however, seems to be betting otherwise. With recent reports hinting that an “Apple Car” could be coming out within the next two-to-four years, the most valuable tech company in the world is starting to make some noise as relates to driverless tech. And to put it in the most straightforward way possible, The Street writes that Apple has patents for virtual reality in autonomous cars.
What does that mean, exactly? Well, the early reports are that it means passengers in an Apple (or possible Apple tech-infused) driverless car will be able to <em>shoot zombies</em> in a VR experience that goes hand-in-hand with the car ride. It’s an idea that almost seems like a joke the first time you read it, and yet it’s one that appears to be very real. And it raises the idea that self-driving cars could be used not just to allow drivers to relax, but specifically to entertain them as they go. One wonders what other VR experiences could possibly work in this sort of situation, and these are a few ideas that come to mind.
Car Chase Shooters – This is a little bit of a creepy concept, because in a way it’s simulating combat between your vehicle and others on the road. But we’ve already taken shooters to incredibly realistic levels, so it’s probably a likely possibility. In fact, if we’re to be battling zombies, we may as well be in first-person, Grand Theft Auto-style shootouts while our self-driving cars steer us along. It would certainly help pass the time, though it could also make riding legitimately scary.
Racing Games – This seems like the obvious choice for a VR game based in a driverless car, though it might be trickier than we imagine. Racing games require pace, and there’s a chance that getting caught up in that kind of pace while your actual car is moving along at what would be a slower and less erratic pace could lead to motion sickness or something similar. That said, if the ride is smooth enough, the fact that you could be sitting in a real car seat, perhaps with a steering wheel-like controller, could make it feel incredibly realistic also.
Casino Games – There’s something to be said for some of the simplest VR experiences making it into cars as well, so as to provide passive entertainment without any of the action and speed that could cause the motion issues mentioned above. Casino gaming could mean simulated poker or blackjack tables, or even slots and arcades that come to life around you. 3D gaming styles have taken over the slot genre already, and a couple of the popular games that have thrived in 3D have been turned into VR experiences already. They’d make for excellent road trip entertainment with relatively little hassle or risk of discomfort.
Audioshield & Fruit Ninja – These are a little bit different because they’re specific games rather than genres. But in a way they’re similar. Fruit Ninja just means slashing fruit as it falls in front of you in 3D space; Audioshield works like VR guitar hero , only with punching motions instead of a plastic guitar. But both mean you’re simply staying in place and reacting to elements coming at you – something that almost sounds downright pleasant as you sit in a comfortable car seat moving along on your way.
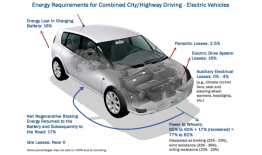
by S.E.Tice…
Battery (only) Electric cars (aka BEVs) cost LESS to Maintain than conventional ICE powered (internal combustion engine) vehicles – this is an universally agreed truth!
(Also true, they cost LESS to Operate for the consumer, partly because they are ~3x more efficient than an ICE powered car, especially if the owner “fuels” up with their own solar electric panels, battery storage, net energy metering. BEVs are the most efficient, as they use 80% of energy onboard to move the car down the road (much higher than conventional powered vehicles) but that subject is for another post)
You would be surprised to learn how many non-Tesla dealership sales people fail to mention either or both of these BEV advantages (BEV – Battery only Electric Vehicle) . BEVs cost less to maintain than conventional vehicles because:
1 – Significantly less mechanical brake maintenance from less wear due to regenerative or dynamic braking. BEVs recapture a portion of their kinetic energy for braking, by using the motor(s) as generator(s) to slow down the vehicle and put that energy back into the battery to extend range – rather than use of their mechanical brakes, which create heat and dust wearing down the pads and their rotors. (Even diesel-electric locomotives use dynamic braking, dissipating their captured energy into resistor banks, because they typically do not have battery banks OR, if they are grid tied, send the energy back to the grid.)
2 – The battery, motor, and associated electronics require little to no regular maintenance. There are fewer fluids to change than in a typical gas/diesel (ICE – internal combustion engine) powered vehicle.
3 – There are far fewer moving parts to wear out relative to a conventional ICE.
Maintenance is one of the 6 contributors to TCO – total cost of ownership. The other 5 are: Purchase, Insurance, Depreciation, Tax and “Fuel” Cost (whether dino-fuel or electric).
2015 study clearly shows lower maintenance costs in four regions around the world. Unfortunately, as far as “fueling costs”, this study does not seem to show the cost advantage of BEV owners fueling their vehicles with their own solar electric panels – https://cleantechnica.com/…/new-study-finds-electric-vehic…/
BEVs also cost less to operate – (regen braking adds 15-20% to the overall efficiency) – https://insideevs.com/bevs-80-percent-energy-move-car/
https://avt.inl.gov/sites/default/files/pdf/fsev/costs.pdf
https://www.ucsusa.org/…/a…/2017/11/cv-report-ev-savings.pdf
https://www.solar-estimate.org/…/2018-03-07-do-electric-veh…